لیست تولید کنندگان شمش فولادی
لیست تولیدکنندگان شمش فولاد
به گزارش «خبرنامه دانشجویان ایران»؛ لیست تولیدکنندگان شمش فولادی برای فعالان صنعت فولاد بازرگانان شرکت های ساختمانی و تولید کنندگان محصولات فولادی بسیار مفید است. آگاهی از مشخصات تولید کنندگان ظرفیت تولید و استانداردهای محصولات به خریداران و سرمایه گذاران کمک می کند تا تأمین کنندگان مناسب را انتخاب کرده و بهترین تصمیم را در خرید و همکاری بگیرند. همچنین این اطلاعات برای برنامه ریزیهای صنعتی و صادراتی نیز کاربرد دارد.قیمت شمش فولاد هم به برند و سطح کیفیت آن وابسته است .
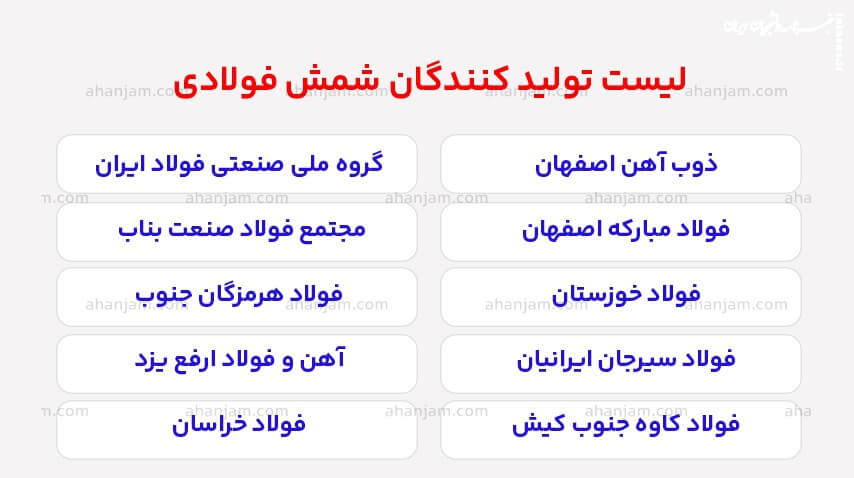
لیست تولیدکنندگان شمش فولادی ایران عبارتند از:
- ذوب آهن اصفهان
- فولاد مبارکه اصفهان
- فولاد خوزستان
- فولاد سیرجان ایرانیان
- فولاد کاوه جنوب کیش
- گروه ملی صنعتی فولاد ایران
- مجتمع فولاد صنعت بناب (شاهین بناب)
- فولاد هرمزگان جنوب
- آهن و فولاد ارفع یزد
- فولاد خراسان
شمش فولادی (Steel Billet) یک محصول نیمه تمام فولادی با سطح مقطع معمولاً مربع یا دایره ای و ابعاد کوچک تر از بلوم و بزرگ تر از میلگرد است. این محصول مستقیماً از فرآیند ریخته گری مداوم (Continuous Casting) به دست می آید و به عنوان ماده اولیه برای تولید محصولات طویل فولادی مانند میلگرد سیم نبشی ناودانی و لوله مورد استفاده قرار می گیرد. عملکرد فنی شمش فولادی را می توان در موارد زیر خلاصه کرد :
- پیش ماده تولید : شمش فولادی گام میانی در زنجیره تولید فولاد است و نقش واسطه ای بین فولاد مذاب و محصولات نهایی را ایفا می کند.
- قابلیت شکل دهی : به دلیل ترکیب شیمیایی و ساختار متالورژیکی کنترل شده شمش فولادی قابلیت شکل دهی و تغییر فرم پذیری بالایی دارد و به راحتی در فرآیندهای نورد گرم و سرد به محصولات مورد نظر تبدیل می شود.
- یکنواختی کیفیت : فرآیند ریخته گری مداوم تولید شمش های فولادی با کیفیت و خواص مکانیکی یکنواخت را تضمین می کند که برای تولید محصولات با کیفیت بالا ضروری است.
- بهره وری تولید : استفاده از شمش فولادی به عنوان ماده اولیه راندمان تولید را در صنایع پایین دستی افزایش می دهد و هزینه های تولید را کاهش می دهد.
تولید شمش فولادی
تولید شمش فولادی فرآیندی چند مرحله ای است که از ذوب مواد اولیه آغاز شده و با شکل دهی و انجماد فولاد مذاب در قالب های مخصوص به پایان می رسد. اجزای اصلی و اصول کارکرد این فرآیند به شرح زیر است :
- مواد اولیه : مواد اولیه اصلی برای تولید شمش فولادی شامل آهن قراضه آهن اسفنجی و آهن خام (Pig Iron) است. ترکیب دقیق مواد اولیه به نوع فولاد مورد نظر و فرآیند ذوب بستگی دارد.
- ذوب فولاد : فولاد مذاب در کوره های مختلفی از جمله کوره های قوس الکتریکی (EAF) و کوره های بلند (Blast Furnace) تولید می شود.
- کوره قوس الکتریکی (EAF) : در این کوره از انرژی الکتریکی برای ذوب قراضه و سایر مواد اولیه استفاده می شود. کوره های قوس الکتریکی برای تولید فولادهای آلیاژی و فولادهای ویژه مناسب هستند و انعطاف پذیری بالایی در انتخاب مواد اولیه دارند. فرآیند ذوب در EAF شامل مراحل شارژ مواد ذوب سرباره گیری اکسیژن دهی و تنظیم ترکیب شیمیایی است.
- کوره بلند (Blast Furnace) : کوره بلند برای تولید آهن خام از سنگ آهن استفاده می شود. آهن خام تولید شده در کوره بلند ماده اولیه اصلی برای تولید فولاد در کوره های اکسیژنی (BOF – Basic Oxygen Furnace) است. فرآیند کوره بلند شامل احتراق کک به عنوان سوخت و عامل احیاکننده و دمیدن هوای گرم برای افزایش دما و سرعت واکنش ها است. آهن مذاب تولید شده از کوره بلند ناخالصی های بیشتری نسبت به فولاد مذاب EAF دارد و نیاز به تصفیه بیشتری در مراحل بعدی دارد.
- متالورژی ثانویه : پس از ذوب فولاد عملیات متالورژی ثانویه برای تنظیم دقیق تر ترکیب شیمیایی حذف ناخالصی ها (مانند گوگرد و فسفر) و بهبود خواص فولاد انجام می شود. این عملیات شامل فرآیندهایی مانند LF (Ladle Furnace) VD (Vacuum Degassing) و RH (Ruhrstahl Heraeus) است.
- کوره پاتیلی (LF) : برای گرمایش مجدد فولاد مذاب تنظیم ترکیب شیمیایی دقیق و همگن سازی دما و ترکیب استفاده می شود. در LF افزودن عناصر آلیاژی سرباره گیری و هم زدن مذاب به منظور بهبود کیفیت فولاد انجام می شود.
- تخلیص خلاء (VD) : برای کاهش میزان گازهای محلول در فولاد مذاب (مانند هیدروژن و اکسیژن) و حذف ناخالصی های فرار استفاده می شود. VD به ویژه برای تولید فولادهای با کیفیت بالا و حساس به هیدروژن ضروری است.
- فرآیند RH : یک فرآیند تخلیص خلاء قوی تر است که علاوه بر گاززدایی قابلیت کربن زدایی و حذف ناخالصی های غیرفلزی را نیز دارد. RH برای تولید فولادهای فوق کم کربن و فولادهای با خواص ویژه کاربرد دارد.
- ریخته گری مداوم (Continuous Casting – CCM) : فولاد مذاب پس از عملیات متالورژی ثانویه به ماشین ریخته گری مداوم منتقل می شود. در CCM فولاد مذاب به طور پیوسته از تاندیش (Tundish) به داخل قالب (Mold) مسی آبگرد سرازیر شده و در حین پایین رفتن منجمد می شود.
- تاندیش : مخزن واسطه ای است که فولاد مذاب را از پاتیل به قالب های ریخته گری منتقل می کند. تاندیش نقش مهمی در توزیع یکنواخت مذاب بین رشته های ریخته گری جداسازی ناخالصی های شناور و حفظ دمای مذاب دارد.
- قالب : قالب مسی آبگرد شکل دهی اولیه شمش فولادی را انجام می دهد و باعث انجماد سطحی مذاب می شود. قالب ها در اشکال و ابعاد مختلف برای تولید شمش های با مقاطع گوناگون طراحی می شوند. جنس قالب ها معمولاً از مس با آلیاژهای خاص است که هدایت حرارتی بالایی داشته و در برابر خوردگی و سایش مقاوم باشند.
- خنک کاری ثانویه : پس از خروج شمش از قالب خنک کاری ثانویه با پاشش آب یا هوا برای تکمیل فرآیند انجماد و رسیدن به دمای مناسب برای برش انجام می شود. سیستم خنک کاری ثانویه شامل نازل های پاشش آب غلتک های هدایت کننده و سیستم کنترل جریان آب است. کنترل دقیق نرخ خنک کاری در این مرحله نقش مهمی در جلوگیری از ایجاد ترک های سطحی و بهبود کیفیت داخلی شمش دارد.
- راست کننده (Straightener) : شمش منجمد شده به تدریج از ماشین ریخته گری خارج می شود و در حین خروج توسط غلتک های راست کننده صاف و مستقیم می شود.
- برش (Cutting) : شمش های فولادی پس از خروج از ماشین ریخته گری و راست شدن به طول های مورد نظر توسط دستگاه های برش اتوماتیک (مانند گیوتین یا اره های دیسکی) بریده می شوند.
- کنترل کیفیت : در طول فرآیند تولید شمش فولادی کنترل کیفیت دقیق و مستمر برای اطمینان از مطابقت محصول با استانداردهای مورد نظر انجام می شود. این کنترل کیفیت شامل بررسی ترکیب شیمیایی خواص مکانیکی ابعاد و کیفیت سطحی شمش ها است. روش های بازرسی غیرمخرب (NDT) مانند آزمایش التراسونیک (UT) و بازرسی ذرات مغناطیسی (MT) برای شناسایی عیوب داخلی و سطحی شمش ها به کار می روند.
کاربردهای شمش فولادی
شمش فولادی به عنوان ماده اولیه در صنایع مختلفی کاربرد دارد. برخی از مهم ترین کاربردهای صنعتی شمش فولادی عبارتند از :
- صنعت ساختمان : شمش فولادی ماده اولیه اصلی برای تولید میلگردهای فولادی است که در بتن مسلح به عنوان عنصر تقویت کننده استفاده می شوند. همچنین شمش فولادی برای تولید پروفیل های ساختمانی مانند نبشی ناودانی و تیرآهن نیز کاربرد دارد.
- صنعت خودروسازی : در صنعت خودروسازی شمش فولادی برای تولید قطعات فورج و ماشین کاری شده مانند میل لنگ میل سوپاپ اتصالات سیستم تعلیق و قطعات گیربکس استفاده می شود. فولادهای آلیاژی تولید شده از شمش استحکام و دوام بالایی را برای قطعات خودرو فراهم می کنند.
- صنعت ماشین سازی : شمش فولادی در تولید قطعات ماشین آلات صنعتی مانند چرخ دنده ها محورها شفت ها یاتاقان ها و قطعات هیدرولیک کاربرد گسترده ای دارد. فولادهای ابزار و فولادهای مهندسی تولید شده از شمش خواص مکانیکی و مقاومت به سایش بالایی را برای قطعات ماشین آلات فراهم می کنند.
- صنعت نفت و گاز : شمش فولادی برای تولید لوله های انتقال نفت و گاز قطعات حفاری و تجهیزات صنایع نفت و گاز استفاده می شود. فولادهای مقاوم به خوردگی و فولادهای با استحکام بالا تولید شده از شمش عملکرد ایمن و قابل اعتماد تجهیزات نفتی و گازی را تضمین می کنند.
- صنعت ریلی : شمش فولادی ماده اولیه برای تولید ریل های راه آهن چرخ های قطار و قطعات سیستم تعلیق واگن ها است. فولادهای ویژه ریلی تولید شده از شمش مقاومت به سایش و خستگی بالایی را در شرایط سخت کاری فراهم می کنند.
مثال های صنعتی :
- کارخانه ذوب آهن اصفهان : یکی از بزرگترین تولیدکنندگان شمش فولادی در ایران است که شمش های فولادی را با گریدهای مختلف برای صنایع ساختمانی خودروسازی و ماشین سازی تولید می کند.
- شرکت فولاد مبارکه اصفهان : علاوه بر ورق های فولادی شمش فولادی نیز تولید می کند و محصولات خود را به صنایع مختلف داخلی و خارجی عرضه می کند.
- شرکت فولاد خوزستان : یکی دیگر از تولیدکنندگان بزرگ شمش فولادی در ایران است که با استفاده از روش کوره قوس الکتریکی شمش های فولادی با کیفیت بالا تولید می کند.
- شرکت های بین المللی مانند ArcelorMittal و Nippon Steel : از بزرگترین تولیدکنندگان فولاد در جهان هستند که حجم قابل توجهی شمش فولادی برای بازارهای جهانی تولید می کنند.
استاندارد های تولید شمش فولادی
تولید و کیفیت شمش فولادی تحت استانداردهای بین المللی متعددی کنترل می شود. برخی از مهم ترین استانداردهای بین المللی مرتبط با شمش فولادی عبارتند از :
- ISO ۶۹۳۵ : استاندارد بین المللی برای میلگردهای فولادی بتن مسلح که مشخصات فنی و روش های آزمون میلگردهای تولید شده از شمش فولادی را تعیین می کند.
- ASTM A۶۱۵/A۶۱۵M : استاندارد آمریکایی برای میلگردهای فولادی بتن مسلح که مشابه استاندارد ISO ۶۹۳۵ است و در آمریکای شمالی و سایر مناطق جهان به طور گسترده استفاده می شود.
- EN ۱۰۰۲۵ : استاندارد اروپایی برای محصولات فولادی گرم نورد شده ساختمانی که شامل مشخصات فنی و الزامات کیفیت برای شمش های فولادی مورد استفاده در سازه های فولادی است.
- JIS G ۳۱۰۱ : استاندارد ژاپنی برای فولادهای ساختمانی عمومی که مشخصات فنی و روش های آزمون شمش های فولادی مورد استفاده در کاربردهای عمومی ساختمانی را تعیین می کند.
فناوری های پیشرفته در تولید شمش فولادی
- ریخته گری با شکل نزدیک به نهایی (Near-Net Shape Casting) : تکنولوژی های پیشرفته ریخته گری مداوم مانند ریخته گری نازک لایه (Thin Slab Casting) و ریخته گری نواری (Strip Casting) امکان تولید شمش های فولادی با ابعاد و شکل های نزدیک به محصول نهایی را فراهم می کنند. این فناوری ها نیاز به فرآیندهای نورد و شکل دهی بعدی را کاهش داده و راندمان تولید و صرفه جویی در انرژی را افزایش می دهند.
- همزن الکترومغناطیسی (Electromagnetic Stirring – EMS) : در فرآیند ریخته گری مداوم استفاده از همزن های الکترومغناطیسی در قالب و ناحیه خنک کاری ثانویه باعث بهبود ساختار انجماد کاهش جدایش عناصر آلیاژی و بهبود کیفیت داخلی شمش می شود. EMS با ایجاد جریان های گردابی در مذاب انتقال حرارت و مواد را بهبود می بخشد و ساختار دندریتی ریزتر و یکنواخت تری را ایجاد می کند.
- سیستم های کنترل اتوماتیک و هوشمند : به کارگیری سیستم های کنترل اتوماتیک و هوشمند مبتنی بر هوش مصنوعی (AI) و یادگیری ماشین (ML) در فرآیند تولید شمش فولادی امکان پایش و کنترل دقیق تر پارامترهای فرآیند بهینه سازی عملکرد تجهیزات و پیش بینی و جلوگیری از وقوع عیوب را فراهم می کند. این سیستم ها با استفاده از داده های سنسورها و اطلاعات فرآیند الگوهای بهینه را شناسایی کرده و تنظیمات فرآیند را به صورت خودکار انجام می دهند.
- دیجیتال سازی و صنعت ۴.۰ : ادغام فناوری های دیجیتال و مفاهیم صنعت ۴.۰ در صنعت فولاد منجر به ایجاد کارخانه های هوشمند و متصل شده است. در این کارخانه ها تمامی مراحل تولید از سفارش گیری تا تحویل محصول به صورت دیجیتالی مدیریت و پایش می شوند. استفاده از اینترنت اشیاء صنعتی (IIoT) ابر محاسباتی (Cloud Computing) و تحلیل داده های بزرگ (Big Data Analytics) امکان بهبود بهره وری کاهش هزینه ها و افزایش انعطاف پذیری تولید را فراهم می کند.
معایب تولید شمش فولادی
تولید شمش فولادی با چالش ها و محدودیت های فنی متعددی روبرو است که نیازمند توجه و راهکارهای مهندسی مناسب هستند. برخی از مهم ترین چالش ها و محدودیت های فنی عبارتند از :
- عیوب سطحی و داخلی : شمش های فولادی ممکن است در طول فرآیند تولید دچار عیوب سطحی مانند ترک های سطحی پوسته شدن و ناهمواری های سطحی و عیوب داخلی مانند تخلخل جدایش عناصر آلیاژی و آخال های غیرفلزی شوند. این عیوب می توانند خواص مکانیکی و عملکرد محصول نهایی را تحت تأثیر قرار دهند. شناسایی و کنترل عوامل ایجاد این عیوب از جمله چالش های اصلی در تولید شمش فولادی با کیفیت بالا است.
- کنترل نرخ انجماد و ساختار دندریتی : کنترل دقیق نرخ انجماد فولاد مذاب در فرآیند ریخته گری مداوم برای دستیابی به ساختار دندریتی ریز و یکنواخت و جلوگیری از تشکیل عیوب انجمادی ضروری است. نرخ انجماد نامناسب می تواند منجر به تشکیل ساختارهای غیریکنواخت جدایش عناصر آلیاژی و افزایش تخلخل شود. بهینه سازی سیستم خنک کاری و استفاده از فناوری های مانند EMS برای کنترل ساختار انجماد از اهمیت بالایی برخوردار است.
- مصرف انرژی و مسائل زیست محیطی : صنعت فولاد از صنایع پرمصرف انرژی و آلاینده محیط زیست به شمار می رود. تولید شمش فولادی نیز مصرف انرژی قابل توجهی دارد و می تواند منجر به انتشار گازهای گلخانه ای و آلاینده های هوا و آب شود. کاهش مصرف انرژی استفاده از منابع انرژی تجدیدپذیر و کاهش آلایندگی های زیست محیطی از چالش های مهم در راستای توسعه پایدار صنعت فولاد است.
- رقابت قیمتی و کیفیت : بازار جهانی فولاد بازاری رقابتی است و تولیدکنندگان شمش فولادی باید همواره تلاش کنند تا محصولات با کیفیت بالا و قیمت رقابتی ارائه دهند. بهبود بهره وری تولید کاهش هزینه ها و افزایش کیفیت محصول از عوامل کلیدی برای موفقیت در این بازار رقابتی است.
نکات مهم در تولید شمش فولادی
برای بهینه سازی و بهبود عملکرد فرآیند تولید شمش فولادی و ارتقاء کیفیت محصول می توان به نکات کلیدی زیر توجه کرد :
- بهینه سازی فرآیند ذوب و متالورژی ثانویه : انتخاب فرآیند ذوب مناسب با توجه به نوع فولاد و مواد اولیه کنترل دقیق پارامترهای فرآیند ذوب و بهینه سازی عملیات متالورژی ثانویه برای حذف ناخالصی ها و تنظیم ترکیب شیمیایی نقش مهمی در بهبود کیفیت فولاد مذاب و شمش تولیدی دارد.
- کنترل دقیق فرآیند ریخته گری مداوم : بهینه سازی طراحی قالب سیستم خنک کاری و سیستم کنترل ماشین ریخته گری مداوم برای دستیابی به نرخ انجماد مناسب جلوگیری از تشکیل عیوب انجمادی و بهبود کیفیت سطحی و داخلی شمش ضروری است. استفاده از سیستم های کنترل اتوماتیک و هوشمند برای پایش و کنترل دقیق پارامترهای فرآیند ریخته گری می تواند به بهبود عملکرد و کاهش ضایعات کمک کند.
- بهره گیری از فناوری های پیشرفته : استفاده از فناوری های پیشرفته مانند ریخته گری با شکل نزدیک به نهایی EMS و سیستم های کنترل هوشمند می تواند به بهبود راندمان تولید کاهش مصرف انرژی و ارتقاء کیفیت شمش فولادی منجر شود. سرمایه گذاری در تحقیق و توسعه و به کارگیری فناوری های نوین از عوامل کلیدی برای رقابت پذیری در صنعت فولاد است.
- تمرکز بر کیفیت مواد اولیه : انتخاب مواد اولیه با کیفیت و کنترل دقیق ترکیب شیمیایی و کیفیت قراضه آهن اسفنجی و آهن خام تأثیر مستقیمی بر کیفیت فولاد مذاب و شمش تولیدی دارد. بهینه سازی زنجیره تأمین مواد اولیه و استفاده از مواد اولیه مرغوب از اهمیت بالایی برخوردار است.
- آموزش و توسعه نیروی انسانی : بهره برداری و نگهداری صحیح از تجهیزات پیشرفته و کنترل دقیق فرآیندهای پیچیده تولید شمش فولادی نیازمند نیروی انسانی متخصص و ماهر است. سرمایه گذاری در آموزش و توسعه دانش و مهارت های کارکنان از عوامل کلیدی برای بهبود عملکرد و افزایش بهره وری در صنعت فولاد است.
سخن آخر
شمش فولادی محصولی استراتژیک و حیاتی در صنایع مختلف است که نقش کلیدی در توسعه زیرساخت ها و صنایع تولیدی ایفا می کند. تولید شمش فولادی با کیفیت بالا و قیمت رقابتی نیازمند درک عمیق اصول مهندسی متالورژی و بهره گیری از فناوری های پیشرفته است.
بهینه سازی فرآیندهای تولید کنترل دقیق کیفیت کاهش مصرف انرژی و توجه به مسائل زیست محیطی از جمله چالش ها و فرصت های پیش روی صنعت تولید شمش فولادی در جهان امروز است. با توجه به روند رو به رشد تقاضای جهانی برای فولاد و توسعه فناوری های نوین در صنعت فولاد انتظار می رود که صنعت تولید شمش فولادی در آینده شاهد پیشرفت های چشمگیری در زمینه بهره وری کیفیت و پایداری باشد.
تحقیقات و نوآوری های مستمر در زمینه مواد اولیه فرآیندهای تولید و فناوری های کنترل کیفیت نقش مهمی در ارتقاء جایگاه صنعت تولید شمش فولادی در اقتصاد جهانی ایفا خواهد کرد.
پرسش و پاسخ های رایج
۱. چه گریدهای مختلفی از شمش فولادی وجود دارد و کاربردهای آنها چیست؟
شمش های فولادی بر اساس ترکیب شیمیایی و خواص مکانیکی به گریدهای مختلفی دسته بندی می شوند. برخی از گریدهای رایج و کاربردهای آنها عبارتند از :
- فولادهای کربنی : شامل فولادهای کم کربن متوسط کربن و پر کربن هستند. فولادهای کم کربن برای تولید میلگرد و پروفیل های ساختمانی فولادهای متوسط کربن برای قطعات ماشین کاری شده و فولادهای پر کربن برای ابزارهای برش و قطعات مقاوم به سایش کاربرد دارند.
- فولادهای آلیاژی : شامل فولادهای کم آلیاژ و پر آلیاژ هستند. فولادهای کم آلیاژ برای قطعات با استحکام بالا و فولادهای پر آلیاژ (مانند فولادهای زنگ نزن و فولادهای ابزار) برای کاربردهای خاص با نیاز به مقاومت به خوردگی حرارت و سایش بالا استفاده می شوند.
۲. روش های اصلی کنترل کیفیت در تولید شمش فولادی کدامند؟
روش های کنترل کیفیت در تولید شمش فولادی شامل موارد زیر است :
- آنالیز شیمیایی : تعیین ترکیب شیمیایی فولاد مذاب و شمش تولیدی برای اطمینان از مطابقت با گرید مورد نظر.
- آزمون های مکانیکی : آزمون های کشش خمش ضربه و سختی برای تعیین خواص مکانیکی شمش و اطمینان از برآورده شدن الزامات استاندارد.
- بازرسی غیرمخرب (NDT) : روش های التراسونیک (UT) ذرات مغناطیسی (MT) مایع نافذ (PT) و رادیوگرافی (RT) برای شناسایی عیوب داخلی و سطحی شمش بدون تخریب آن.
- بازرسی چشمی : بررسی سطحی شمش برای شناسایی عیوب سطحی مانند ترک ها پوسته شدن و ناهمواری ها.
۳. ملاحظات زیست محیطی در تولید شمش فولادی چیست؟
صنعت فولاد از صنایع آلاینده محیط زیست است و تولید شمش فولادی نیز ملاحظات زیست محیطی خاص خود را دارد :
- انتشار گازهای گلخانه ای : کوره های ذوب فولاد و فرآیندهای احتراق گازهای گلخانه ای مانند دی اکسید کربن (CO۲) را منتشر می کنند که به تغییرات آب و هوایی دامن می زند.
- آلودگی هوا : انتشار ذرات معلق اکسیدهای گوگرد (SOx) و اکسیدهای نیتروژن (NOx) از فرآیندهای تولید فولاد می تواند کیفیت هوا را کاهش داده و به سلامت انسان و محیط زیست آسیب برساند.
- آلودگی آب : پساب های صنعتی حاوی فلزات سنگین و مواد شیمیایی از فرآیندهای تولید فولاد می توانند منابع آب را آلوده کنند.
- مصرف منابع طبیعی : تولید فولاد نیازمند مصرف مقادیر زیادی آب انرژی و مواد اولیه معدنی است که می تواند به تخریب منابع طبیعی منجر شود.
برای کاهش اثرات زیست محیطی تولید شمش فولادی اقدامات زیر ضروری است :
- بهینه سازی مصرف انرژی و استفاده از انرژی های تجدیدپذیر.
- به کارگیری فناوری های کنترل آلودگی هوا و آب.
- افزایش بازیافت قراضه فولادی و کاهش مصرف مواد اولیه بکر.
- مدیریت پسماند و کاهش تولید پسماندهای صنعتی.
- توسعه فناوری های تولید فولاد سبز با کمترین اثرات زیست محیطی.