نقش کلیدی آمونیاک در کشاورزی؛ از تولید کود تا بهبود رشد گیاهان
آمونیاک در صنایع شیمیایی؛ تولید ویژگی ها و واکنش های مهم
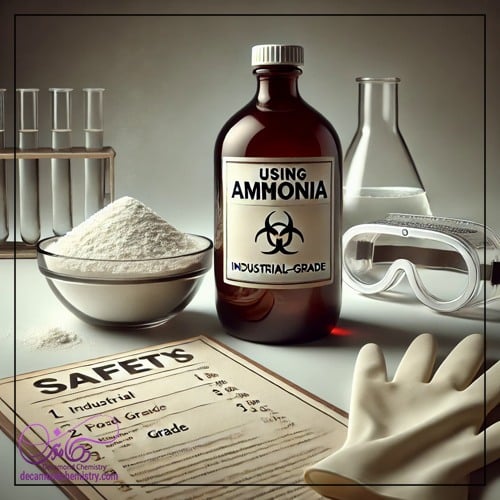
آمونیاک مولکولی حیاتی با فرمول شیمیایی NH₃ نه تنها پایه و اساس تولید کودهای شیمیایی برای تامین غذای جمعیت رو به رشد جهان است بلکه به عنوان یک ماده اولیه کلیدی در طیف گسترده ای از صنایع شیمیایی نیز نقش محوری ایفا می کند. این ترکیب شیمیایی با خواص منحصربه فرد و واکنش پذیری بالا امکان تولید محصولات متنوعی از مواد منفجره و الیاف مصنوعی گرفته تا داروها و مواد شوینده را فراهم می آورد. در این مقاله به بررسی جامع آمونیاک در صنایع شیمیایی از فرآیندهای تولید صنعتی و ویژگی های اساسی آن گرفته تا واکنش های مهم کاربردهای گسترده و استانداردهای مرتبط پرداخته می شود.
تولید صنعتی آمونیاک : فرآیند هابر-بوش و فناوری های نوین
تولید صنعتی آمونیاک عمدتاً از طریق فرآیند هابر-بوش انجام می شود که یکی از مهم ترین دستاوردهای مهندسی شیمی در قرن بیستم به شمار می رود. این فرآیند که در اوایل قرن بیستم توسط فریتز هابر و کارل بوش توسعه یافت امکان سنتز آمونیاک از نیتروژن موجود در هوا و هیدروژن را در مقیاس صنعتی فراهم کرد.
اصول کارکرد فرآیند هابر-بوش :
فرآیند هابر-بوش بر اساس واکنش تعادلی زیر استوار است :
N₂(g) + ۳H₂(g) ⇌ ۲NH₃(g) ΔH = -۹۲ kJ/mol
این واکنش گرماده است و در دماهای بالا و فشارهای بالا به سمت تشکیل آمونیاک پیش می رود. با این حال سرعت واکنش در دماهای پایین تر به طور قابل توجهی کاهش می یابد. برای حل این مشکل از کاتالیزورهای مبتنی بر آهن استفاده می شود که سرعت واکنش را در دماهای نسبتاً پایین (حدود ۴۰۰-۵۰۰ درجه سانتیگراد) افزایش می دهند.
اجزای اصلی واحد تولید آمونیاک به روش هابر-بوش :
- تولید گاز سنتز (Synthesis Gas) : گاز سنتز مخلوطی از هیدروژن و نیتروژن با نسبت مولی ۳ : ۱ است. این گاز معمولاً از ریفورمینگ بخار متان (واکنش متان با بخار آب) یا گازی سازی زغال سنگ تولید می شود. در ریفورمینگ بخار متان گاز طبیعی (عمدتاً متان) با بخار آب در حضور کاتالیزور نیکل در دماهای بالا واکنش می دهد و گاز سنتز تولید می شود.
CH₄(g) + H₂O(g) ⇌ CO(g) + ۳H₂(g)
سپس واکنش جابجایی آب-گاز برای افزایش نسبت هیدروژن و کاهش مقدار مونوکسید کربن انجام می شود.
CO(g) + H₂O(g) ⇌ CO₂(g) + H₂(g)
دی اکسید کربن تولید شده در این مرحله معمولاً با استفاده از روش های جذب شیمیایی یا فیزیکی جدا می شود. نیتروژن مورد نیاز نیز معمولاً از تقطیر جزء به جزء هوا به دست می آید.
- تصفیه گاز سنتز : گاز سنتز تولید شده حاوی ناخالصی هایی مانند مونوکسید کربن دی اکسید کربن بخار آب و ترکیبات گوگردی است که می توانند کاتالیزور را مسموم کنند. بنابراین گاز سنتز قبل از ورود به راکتور سنتز آمونیاک تحت فرآیندهای تصفیه دقیق قرار می گیرد. این فرآیندها شامل جذب تبدیل کاتالیزوری و متان سازی برای حذف ناخالصی ها است.
- راکتور سنتز آمونیاک : راکتور سنتز آمونیاک قلب واحد تولید آمونیاک است. در این راکتور گاز سنتز تصفیه شده در دما و فشار بالا و در حضور کاتالیزور آهن به آمونیاک تبدیل می شود. راکتورهای صنعتی معمولاً از نوع بستر ثابت چند مرحله ای هستند و برای کنترل دما و فشار به دقت طراحی شده اند. فشار در راکتورهای هابر-بوش معمولاً بین ۱۵۰ تا ۲۵۰ بار و دما بین ۴۰۰ تا ۵۰۰ درجه سانتیگراد است. کاتالیزورهای مورد استفاده معمولاً اکسید آهن مغناطیسی (Fe₃O₄) هستند که با اکسیدهای پتاسیم کلسیم و آلومینیوم تقویت شده اند.
- جداسازی آمونیاک : آمونیاک تولید شده از راکتور به صورت مخلوطی با گازهای واکنش نکرده (نیتروژن و هیدروژن) خارج می شود. آمونیاک به دلیل نقطه جوش بالا (-۳۳ درجه سانتیگراد) به راحتی از مخلوط گازی با استفاده از میعان و تقطیر جدا می شود. گازهای واکنش نکرده دوباره به راکتور بازگردانده می شوند تا راندمان فرآیند افزایش یابد.
- ذخیره سازی و انتقال آمونیاک : آمونیاک مایع معمولاً در مخازن تحت فشار و در دماهای پایین ذخیره و به محل های مصرف منتقل می شود. استانداردهای ایمنی سختگیرانه ای برای ذخیره سازی و حمل و نقل آمونیاک وجود دارد تا از نشت و خطرات احتمالی جلوگیری شود.
فناوری های نوین در تولید آمونیاک :
در سال های اخیر تحقیقات گسترده ای برای توسعه فناوری های نوین تولید آمونیاک با مصرف انرژی کمتر و اثرات زیست محیطی پایین تر انجام شده است. برخی از این فناوری ها عبارتند از :
- فرآیند هابر-بوش با کاتالیزورهای پیشرفته : توسعه کاتالیزورهای جدید با فعالیت و گزینش پذیری بالاتر می تواند دمای واکنش و در نتیجه مصرف انرژی را کاهش دهد. کاتالیزورهای مبتنی بر روتنیم و نانومواد از جمله گزینه های перспективی هستند.
- تولید آمونیاک الکتروشیمیایی : این روش که به عنوان آمونیاک سبز نیز شناخته می شود از الکترولیز آب برای تولید هیدروژن و از الکتروکاتالیز برای احیای نیتروژن به آمونیاک در شرایط محیطی یا نزدیک به محیطی استفاده می کند. این روش پتانسیل قابل توجهی برای تولید آمونیاک پایدار و غیرمتمرکز دارد به خصوص اگر از انرژی های تجدیدپذیر برای تامین برق استفاده شود.
- فرآیندهای بیولوژیکی تولید آمونیاک : برخی از میکروارگانیسم ها قادر به تثبیت نیتروژن و تولید آمونیاک در شرایط محیطی هستند. تحقیقات در این زمینه در حال انجام است تا روش های بیولوژیکی کارآمدی برای تولید آمونیاک توسعه یابد.
ویژگی های فیزیکی و شیمیایی آمونیاک : از ساختار مولکولی تا خواص منحصربه فرد
آمونیاک یک گاز بی رنگ با بوی تند و زننده است. در شرایط استاندارد دما و فشار به صورت گاز وجود دارد اما به راحتی به مایع تبدیل می شود. آمونیاک مایع بی رنگ و بسیار فرار است.
ویژگی های فیزیکی مهم آمونیاک :
- فرمول مولکولی : NH₃
- جرم مولی : ۱۷.۰۳ گرم بر مول
- نقطه جوش : -۳۳.۳۴ درجه سانتیگراد
- نقطه ذوب : -۷۷.۷۳ درجه سانتیگراد
- چگالی گاز در شرایط استاندارد : ۰.۷۷۱ گرم بر لیتر (سبک تر از هوا)
- چگالی مایع در نقطه جوش : ۰.۶۸۱۹ گرم بر سانتی متر مکعب
- انحلال پذیری در آب : بسیار بالا (تشکیل محلول آمونیاک یا هیدروکسید آمونیوم)
ویژگی های شیمیایی مهم آمونیاک :
- مولکول قطبی : مولکول آمونیاک دارای ساختار هرمی مثلثی است و به دلیل اختلاف الکترونگاتیویته بین نیتروژن و هیدروژن قطبی است. این قطبیت باعث انحلال پذیری بالای آن در آب و سایر حلال های قطبی می شود.
- باز ضعیف : آمونیاک یک باز ضعیف است و در آب با دریافت یک پروتون (H⁺) از آب یون آمونیوم (NH₄⁺) و یون هیدروکسید (OH⁻) تولید می کند.
NH₃(aq) + H₂O(l) ⇌ NH₄⁺(aq) + OH⁻(aq)
محلول آبی آمونیاک خاصیت قلیایی دارد و می تواند با اسیدها واکنش داده و نمک های آمونیوم را تشکیل دهد.
- واکنش پذیری بالا : آمونیاک به دلیل وجود جفت الکترون غیرپیوندی روی اتم نیتروژن بسیار واکنش پذیر است و در واکنش های متعددی شرکت می کند. از جمله واکنش های مهم آمونیاک می توان به موارد زیر اشاره کرد :
- واکنش با اسیدها : تشکیل نمک های آمونیوم (به عنوان مثال واکنش با اسید کلریدریک برای تولید کلرید آمونیوم)
- واکنش با اکسیژن : سوختن در هوا و تشکیل نیتروژن و آب (یا اکسیدهای نیتروژن در شرایط خاص)
- واکنش با فلزات : تشکیل آمیدها و نیتریدها (به عنوان مثال واکنش با سدیم برای تولید آمید سدیم)
- واکنش با ترکیبات آلی : شرکت در واکنش های آمیناسیون آلکیلاسیون و آسیلاسیون برای تولید آمین ها آمیدها و سایر ترکیبات آلی نیتروژن دار.
- واکنش با هالوژن ها : تشکیل هالیدهای نیتروژن و آمونیوم (به عنوان مثال واکنش با کلر برای تولید کلرید نیتروژن)
واکنش های کلیدی آمونیاک در صنایع شیمیایی : از کودهای شیمیایی تا پلیمرها
آمونیاک به عنوان یک ماده اولیه کلیدی در طیف وسیعی از واکنش های شیمیایی در صنایع مختلف به کار می رود. برخی از مهم ترین واکنش های آمونیاک و کاربردهای صنعتی آن ها عبارتند از :
- تولید کودهای شیمیایی : بیشترین کاربرد آمونیاک در تولید کودهای نیتروژنه است. آمونیاک به طور مستقیم به عنوان کود (آمونیاک بی آب) استفاده می شود یا به عنوان ماده اولیه برای تولید سایر کودهای نیتروژنه مانند اوره (CO(NH₂)₂) نیترات آمونیوم (NH₄NO₃) سولفات آمونیوم ((NH₄)₂SO₄) و فسفات آمونیوم (NH₄H₂PO₄) به کار می رود. کودهای نیتروژنه نقش حیاتی در افزایش بهره وری کشاورزی و تامین غذای جمعیت جهان دارند.
- تولید اسید نیتریک (HNO₃) : آمونیاک از طریق فرآیند اوستوالد به اسید نیتریک تبدیل می شود. اسید نیتریک ماده اولیه مهمی برای تولید نیترات ها (مانند نیترات آمونیوم که در کودها و مواد منفجره کاربرد دارد) مواد منفجره (مانند TNT و نیتروگلیسیرین) الیاف نایلون و پلی یورتان ها است.
- تولید مواد منفجره : آمونیاک به عنوان ماده اولیه در تولید انواع مواد منفجره مانند نیترات آمونیوم TNT (تری نیتروتولوئن) و نیتروگلیسیرین به کار می رود. این مواد منفجره در صنایع نظامی معدن کاری و ساخت و ساز کاربرد دارند.
- تولید الیاف مصنوعی : آمونیاک در تولید برخی از الیاف مصنوعی مانند نایلون و آکریلونیتریل نقش دارد. نایلون یک پلی آمید مهم است که در تولید الیاف نساجی پلاستیک های مهندسی و فیلم های پلیمری کاربرد دارد. آکریلونیتریل ماده اولیه برای تولید الیاف اکریلیک است که در صنعت نساجی به طور گسترده استفاده می شود.
- تولید پلی یورتان ها : آمونیاک در تولید دی ایزوسیانات ها که مواد اولیه کلیدی برای تولید پلی یورتان ها هستند به کار می رود. پلی یورتان ها دسته ای از پلیمرهای متنوع هستند که در تولید فوم های عایق الاستومرها پوشش ها چسب ها و الیاف کاربرد دارند.
- تولید داروها و مواد شیمیایی کشاورزی : آمونیاک به عنوان یک واسطه شیمیایی در سنتز بسیاری از داروها و مواد شیمیایی کشاورزی (مانند علف کش ها و حشره کش ها) به کار می رود. ترکیبات نیتروژن دار نقش مهمی در ساختار بسیاری از داروهای مهم ایفا می کنند.
- تصفیه گازهای خروجی : آمونیاک در فرآیندهای حذف اکسیدهای نیتروژن (NOx) از گازهای خروجی نیروگاه ها و صنایع به کار می رود. فرآیندهای کاهش کاتالیزوری انتخابی (SCR) و کاهش غیرکاتالیزوری انتخابی (SNCR) با استفاده از آمونیاک NOx را به نیتروژن و آب تبدیل می کنند و به کاهش آلودگی هوا کمک می کنند.
- صنایع پالایش نفت و گاز : آمونیاک در صنایع پالایش نفت و گاز برای خنثی سازی اسیدهای نفتی کنترل خوردگی و تصفیه گازهای ترش (حاوی سولفید هیدروژن) به کار می رود.
- صنایع لاستیک و پلاستیک : آمونیاک در تولید مواد افزودنی لاستیک و پلاستیک به کار می رود.
- صنایع غذایی و نوشیدنی : آمونیاک به عنوان مبرد در سیستم های تبرید صنعتی و تجاری استفاده می شود. همچنین در برخی از فرآیندهای تصفیه آب و کنترل pH در صنایع غذایی کاربرد دارد.
استانداردهای بین المللی و ملاحظات ایمنی در تولید و حمل و نقل آمونیاک
تولید ذخیره سازی حمل و نقل و استفاده از آمونیاک تحت استانداردهای بین المللی و مقررات ایمنی سختگیرانه ای قرار دارد. آمونیاک یک ماده سمی و خورنده است و تماس با آن می تواند باعث تحریک پوست چشم و دستگاه تنفسی شود. در غلظت های بالا استنشاق آمونیاک می تواند کشنده باشد. همچنین آمونیاک قابل اشتعال است و مخلوط آن با هوا می تواند منفجره باشد.
استانداردهای بین المللی مرتبط با آمونیاک :
- ISO ۸۱۷ : ۲۰۱۴ : مبردها – نامگذاری و طبقه بندی ایمنی
- ANSI K۶۱.۱–۱۹۹۹ : استاندارد ایمنی برای سیستم های تبرید آمونیاکی
- EN ۳۷۸–۱ : ۲۰۱۶ : سیستم های تبرید و پمپ های حرارتی – الزامات ایمنی و زیست محیطی – قسمت ۱ : الزامات اساسی تعاریف طبقه بندی و معیارهای انتخاب
- NFPA ۷۰۴ : سیستم شناسایی خطرات مواد برای واکنش اضطراری
ملاحظات ایمنی در تولید و حمل و نقل آمونیاک :
- طراحی ایمن واحد تولید : واحدهای تولید آمونیاک باید بر اساس اصول مهندسی ایمنی طراحی و ساخته شوند و دارای سیستم های کنترل و ایمنی پیشرفته باشند تا از نشت و حوادث جلوگیری شود.
- آموزش و ایمنی پرسنل : پرسنل شاغل در واحدهای تولید ذخیره سازی و حمل و نقل آمونیاک باید به طور کامل آموزش دیده و با خطرات و روش های ایمنی کار با آمونیاک آشنا باشند.
- استفاده از تجهیزات حفاظت فردی (PPE) : پرسنل باید در هنگام کار با آمونیاک از تجهیزات حفاظت فردی مناسب مانند ماسک تنفسی دستکش عینک ایمنی و لباس محافظ استفاده کنند.
- سیستم های تشخیص و هشدار نشت : واحدهای تولید و ذخیره سازی آمونیاک باید مجهز به سیستم های تشخیص و هشدار نشت آمونیاک باشند تا در صورت بروز نشت اقدامات لازم به سرعت انجام شود.
- پاسخ اضطراری : برنامه های پاسخ اضطراری جامع باید برای مقابله با حوادث احتمالی نشت آمونیاک تدوین و اجرا شوند.
- حمل و نقل ایمن : حمل و نقل آمونیاک باید با استفاده از تانکرهای مخصوص و تحت شرایط ایمنی دقیق انجام شود. مسیرهای حمل و نقل باید با دقت برنامه ریزی شوند تا از مناطق پرجمعیت و حساس اجتناب شود.
چالش ها و محدودیت های فنی
علی رغم اهمیت و کاربردهای گسترده آمونیاک تولید و استفاده از آن با چالش ها و محدودیت های فنی متعددی همراه است :
- مصرف انرژی بالا در فرآیند هابر-بوش : فرآیند هابر-بوش به دلیل نیاز به دما و فشار بالا مصرف انرژی بسیار زیادی دارد و حدود ۱-۲ درصد از مصرف انرژی جهانی را به خود اختصاص می دهد. این امر باعث انتشار قابل توجه گازهای گلخانه ای و تاثیر منفی بر محیط زیست می شود.
- وابستگی به سوخت های فسیلی : بیشتر هیدروژن مورد نیاز برای فرآیند هابر-بوش از سوخت های فسیلی (به ویژه گاز طبیعی) تولید می شود. این وابستگی به سوخت های فسیلی باعث افزایش انتشار دی اکسید کربن و نگرانی های مربوط به پایداری می شود.
- مشکلات کاتالیزوری : کاتالیزورهای آهن مورد استفاده در فرآیند هابر-بوش در دماهای بالا و در حضور ناخالصی ها به تدریج غیرفعال می شوند. این امر نیاز به تعویض دوره ای کاتالیزور و افزایش هزینه های عملیاتی را به همراه دارد.
- خطرات ایمنی : آمونیاک یک ماده سمی خورنده و قابل اشتعال است و خطرات ایمنی جدی در تولید ذخیره سازی حمل و نقل و استفاده از آن وجود دارد. نشت آمونیاک می تواند منجر به حوادث جدی و آسیب های زیست محیطی شود.
- محدودیت های فرآیندهای نوین : فناوری های نوین تولید آمونیاک مانند آمونیاک الکتروشیمیایی و فرآیندهای بیولوژیکی هنوز در مراحل توسعه و تجاری سازی اولیه قرار دارند و برای جایگزینی فرآیند هابر-بوش در مقیاس صنعتی نیاز به تحقیقات و توسعه بیشتر دارند.
نکات کلیدی برای بهینه سازی و بهبود عملکرد
برای بهینه سازی و بهبود عملکرد فرآیندهای تولید و استفاده از آمونیاک می توان اقدامات زیر را انجام داد :
- بهینه سازی فرآیند هابر-بوش : بهبود راندمان فرآیند هابر-بوش از طریق بهینه سازی شرایط عملیاتی (دما فشار نسبت واکنش دهنده ها) استفاده از کاتالیزورهای پیشرفته تر و بازیابی حرارت می تواند مصرف انرژی و هزینه ها را کاهش دهد.
- توسعه منابع هیدروژن پایدار : جایگزینی هیدروژن تولید شده از سوخت های فسیلی با هیدروژن سبز تولید شده از منابع تجدیدپذیر (مانند الکترولیز آب با استفاده از انرژی خورشیدی یا بادی) می تواند انتشار دی اکسید کربن را به طور قابل توجهی کاهش دهد و تولید آمونیاک را پایدارتر کند.
- تحقیق و توسعه کاتالیزورهای نوین : توسعه کاتالیزورهای جدید با فعالیت گزینش پذیری و پایداری بالاتر می تواند دمای واکنش را کاهش دهد سرعت واکنش را افزایش دهد و طول عمر کاتالیزور را بهبود بخشد. نانومواد و کاتالیزورهای مبتنی بر روتنیم از جمله زمینه های перспективی برای تحقیق هستند.
- بهبود ایمنی و کاهش خطرات : بهبود سیستم های ایمنی آموزش پرسنل استفاده از فناوری های تشخیص نشت پیشرفته و اجرای برنامه های پاسخ اضطراری جامع می تواند خطرات ایمنی مرتبط با آمونیاک را کاهش دهد.
- توسعه فرآیندهای نوین تولید آمونیاک : سرمایه گذاری در تحقیق و توسعه فرآیندهای نوین تولید آمونیاک مانند آمونیاک الکتروشیمیایی و فرآیندهای بیولوژیکی می تواند راه را برای تولید آمونیاک پایدارتر و غیرمتمرکزتر هموار کند.
- بازیابی و استفاده مجدد از آمونیاک : در برخی از صنایع آمونیاک به عنوان محصول جانبی یا پسماند تولید می شود. بازیابی و استفاده مجدد از این آمونیاک می تواند به کاهش مصرف آمونیاک تازه و کاهش اثرات زیست محیطی کمک کند.
نتیجه گیری
آمونیاک به عنوان یک ماده شیمیایی حیاتی نقش اساسی در صنایع مختلف ایفا می کند و به ویژه در تامین غذای جمعیت رو به رشد جهان از طریق تولید کودهای شیمیایی اهمیت ویژه ای دارد. فرآیند هابر-بوش با وجود مصرف انرژی بالا همچنان روش اصلی تولید صنعتی آمونیاک است. با این حال چالش های مربوط به پایداری و اثرات زیست محیطی ضرورت توسعه فناوری های نوین و بهینه سازی فرآیندهای موجود را بیش از پیش آشکار می سازد. تحقیقات و توسعه در زمینه های کاتالیزورهای پیشرفته منابع هیدروژن پایدار و فرآیندهای تولید آمونیاک الکتروشیمیایی کلید دستیابی به تولید آمونیاک پایدارتر ایمن تر و کارآمدتر در آینده خواهد بود. آمونیاک همچنان به عنوان یک سنگ بنای اساسی در صنایع شیمیایی باقی خواهد ماند و نقش آن در توسعه پایدار و تامین نیازهای جهانی در آینده پررنگ تر خواهد شد.
پرسش و پاسخ
پرسش ۱ : آیا آمونیاک برای محیط زیست خطرناک است؟
پاسخ : بله آمونیاک می تواند برای محیط زیست خطرناک باشد اگر به درستی مدیریت نشود. نشت آمونیاک به هوا می تواند باعث آلودگی هوا و تشکیل باران اسیدی شود. ورود آمونیاک به آب های سطحی می تواند باعث اوتروفیکاسیون (رشد بی رویه جلبک ها و گیاهان آبزی) و کاهش اکسیژن محلول در آب شود که برای زندگی آبزیان مضر است. همچنین تولید آمونیاک از طریق فرآیند هابر-بوش با مصرف انرژی بالا و انتشار گازهای گلخانه ای همراه است. با این حال با استفاده از فناوری های نوین و مدیریت صحیح می توان اثرات زیست محیطی آمونیاک را به حداقل رساند.
پرسش ۲ : آیا امکان تولید آمونیاک در مقیاس کوچک و غیرمتمرکز وجود دارد؟
پاسخ : بله فناوری های نوین مانند آمونیاک الکتروشیمیایی امکان تولید آمونیاک در مقیاس کوچک و غیرمتمرکز را فراهم می کنند. این روش ها که از انرژی های تجدیدپذیر برای تامین برق و مواد اولیه استفاده می کنند می توانند برای تولید آمونیاک در مناطق دورافتاده و برای کاربردهای خاص مناسب باشند. تولید غیرمتمرکز آمونیاک می تواند وابستگی به واحدهای تولید بزرگ و حمل و نقل طولانی مدت را کاهش دهد و پایداری زنجیره تامین آمونیاک را افزایش دهد.
پرسش ۳ : آیا آمونیاک می تواند جایگزین سوخت های فسیلی شود؟
پاسخ : آمونیاک به عنوان یک حامل انرژی پتانسیل جایگزینی بخشی از سوخت های فسیلی را دارد. آمونیاک می تواند به طور مستقیم به عنوان سوخت در موتورهای احتراق داخلی و توربین های گازی استفاده شود یا به عنوان ماده اولیه برای تولید هیدروژن برای **پی
این کود اوره که همه جا تعریفشو میکنن دقیقا چجوری تو خاک عمل میکنه؟ یه کم علمی تر توضیح بدین ما هم بفهمیم.
من خودم کشاورزم سالهاست دارم از کودهای آمونیاکی استفاده میکنم واقعا تاثیرش عالیه. ولی خب قیمتش خیلی بالاست.
این استانداردهای بین المللی که میگین تو ایران هم رعایت میشه؟ یا فقط حرفه؟
مقاله خیلی خوبی بود واقعا نمیدونستم آمونیاک اینقدر کاربرد داره تو کشاورزی. دستتون درد نکنه.
این کودهای کنترل شده رهش واقعا انقدر که میگن خوبن؟ کسی تجربه استفاده داشته؟
میگن آمونیاک برای محیط زیست خیلی ضرر داره این درسته؟ پس چرا انقدر استفاده میشه؟
من فکر میکردم فقط کودهای شیمیایی هستن که نیتروژن دارن نمیدونستم آمونیاک هم این وسط نقش داره.
این فرآیند هابر بوش که میگین خیلی پیچیده به نظر میرسه. واقعا انقدر مهمه؟
چرا انقدر روی کود اوره تاکید کردین؟ کودهای دیگه نیتروژنی به همون اندازه مهم نیستن؟
این قسمت کاربردهای صنعتی آمونیاک خیلی جالب بود مخصوصا ضدعفونی خاک.
فقط گرونی کود مونده بود که اونم به لطف همین آمونیاک روز به روز داره بیشتر میشه! کی میخواد جواب این کشاورز بدبخت رو بده؟
به نظر من مقاله یکم زیادی طولانی بود میشد خلاصه تر و مفیدتر باشه.
من شنیدم آمونیاک خیلی خطرناکه مگه میشه انقدر راحت تو کشاورزی استفاده بشه؟
این فناوری کشاورزی دقیق که میگین تو ایران هم هست؟ کسی استفاده میکنه؟
این کودهای آمونیاکی مایع برای همه نوع خاک مناسبن؟ یا فقط خاک های خاصی؟
به نظرم مقاله یکم زیادی جنبه مثبت آمونیاک رو نشون داده باید به جنبه های منفی و مشکلاتش هم بیشتر اشاره میکردین.
این سوال و جواب آخر مقاله خیلی خوب بود خیلی از سوالات منو جواب داد.
من دنبال اطلاعات عملی تر بودم مثلا نحوه استفاده از کودهای آمونیاکی تو مزرعه این مقاله بیشتر تئوری بود.
این سوال و جواب آخر مقاله خیلی خوب بود خیلی از سوالات منو جواب داد.
با این همه چالش و محدودیت فنی که گفتین واقعا آمونیاک آینده داره تو کشاورزی؟
با این همه چالش و محدودیت فنی که گفتین واقعا آمونیاک آینده داره تو کشاورزی؟